|
 |
As a substitute for the more costly
process of inlaying with precious or semiprecious stones,
enamelwork (falang 琺瑯) was developed
to give the surface of metal objects a vitreous glaze by
intense heat to create a brilliantly coloured decorative
effect. Enamel is a kind of soft glass, compounded of
flint or sand, red lead, and soda or potassium. These
materials are melted together, producing an almost clear
glass flux with a slighly bluish or greenish tinge. Clear
flux is the base from which coloured enamels are made,
the colouring agent being a metallic oxide, introduced
into the flux when it is in a molten state. Otherwise,
the addition of calx, a mixture of tin and calcined lead,
renders translucent enamels opaque. Solidified "cakes"
of cooled enamel are pulverized into a fine powder. The
powder then is spread on the metal object's surface and
is dried in front of the furnace before introduced into
the muffle of the furnace itself. The vessel being heated
to the point at which the enamel fuses and adheres to its
metal base, the firing of enamel takes only a few minutes.
Painted enamels in China are also called Canton enamels
as this city was the principal seat of their manufacture.
This technique is directly influenced by Western art, and
a great part of Canton enamels was indeed produced for
export. The Chinese called the painted enamel "Western
porcelain" (yangci 洋瓷), the decoration
"Western colors" (yangcai 洋彩) as
it is very different from the traditional Chinese motifs
and colors. Painted enamels are made by laying a ground
of opaque enamel, generally white or opaque, and on this
the main colors are superimposed and fired.
Cloisonné (qiasi falang
掐絲琺瑯) is a special technique, by which thin
strips of metal are bent and curved to follow the outline
of a decorative pattern. They are then soldered to the
surface of the metal object, forming miniature walls that
meet and create little cells between them. Into these
cells, powdered enamel is laid and fused. After is has
cooled, the surface can be polished to remove
imperfections. Champlevé is the opposite process
of cloisonné technique: The surface of the object
is gouded away, creating channels that form the outline
of the design, and that are filled with the enamel powder.
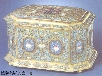 |
This golden box from the Qing time 清, not square, but octogonal with eight faces, is only partially covered with enamel. |
 |
This gourd shaped vase from Qing time is an example
for enamel painting and clearly demonstrates the
porcelain like quality of the enamel technique. |
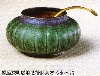 |
A small cup with bowed spoon to insert water into the
ink stone. The spoon only contains a minimum of water and
allows the painter or writer to mix the grounded ink
exactly with the amount of water needed. |
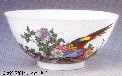 |
Two examples shall show that Qing Dynasty bowls were not purely an industrial mass product of mean quality like we know them from the China food shop from the corner. While the bowl to the left shows us five different kinds of flowers on a coral red ground, the bowl to the right is partially covered with an enamel drawing of a pheasant among peony flowers. |
 |
A zun 尊 type cloisonne vessel, giving a
good example for an old shape revived with new materials,
during Qing time. Today, cloisonne work is very popular
and used for every kind of metal objects, like little
boxes, bowls, chopsticks, or figurines with animal shapes. |
|
|
|